Optimization of production processes
Knowledge, data and experience - together with the customer we analyze production and eliminate losses at the source
Bottleneck detection
Together with the customer, we identify places that limit the fluidity and efficiency of production
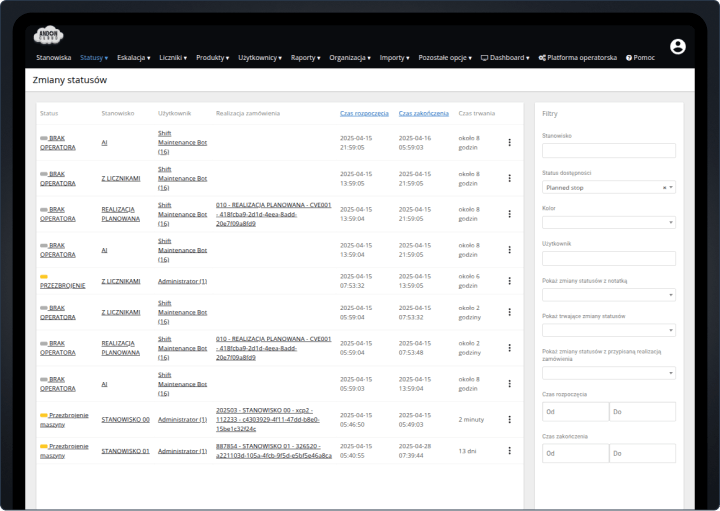
Location of points limiting capacity
Analysis of the times between operations and the frequency of downtime makes it possible to identify specific positions that require intervention
Verification of real line capabilities
The data collected shows how long each operation takes and whether the actual performance matches the planning assumptions
Work with the team to eliminate blockages
We don't just provide data - we help the client plan specific improvement actions based on observations
Reduction of downtime and stops
We support the elimination of the causes of detentions through data analysis and operational activities - not just reporting
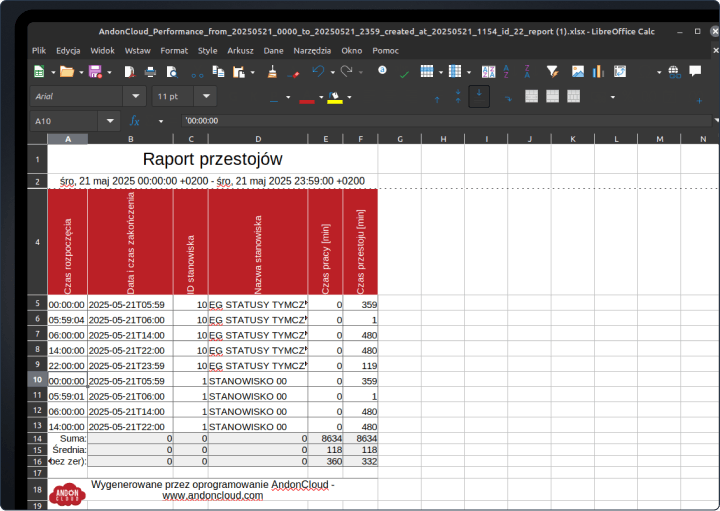
Mapping the causes of stops and micro stops
With precise record-keeping, it is possible to separate short and long outages and their actual cause
Support in interpreting data from the hall
Together with the client, we analyze what is behind the data - we do not leave the user alone with the charts
Implement measures to eliminate problems at the source
We help the team define organizational, process or technical changes that realistically reduce downtime
Reduce changeover times
We work with the customer to standardize and measure changeovers to reduce time and their impact on availability
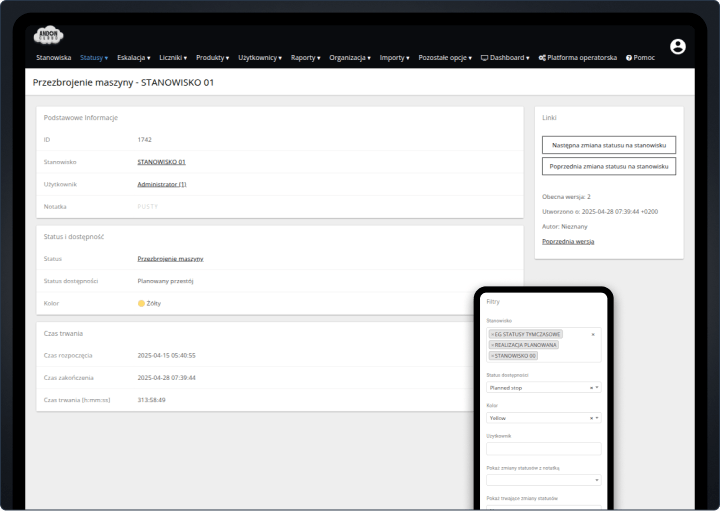
Measurement and comparison of changeover times
The system allows you to record each stage of changeover - the operator can record each event
Identify differences between shifts, orders and products
From the data, you can see if changeovers are longer with specific shifts, people or job types
Standardize and shorten the sequence of activities
We help the customer develop a repeatable changeover pattern and identify redundant or inefficient steps
Support for operational and planning decisions
We provide data and help the management team make decisions based on the real situation in production
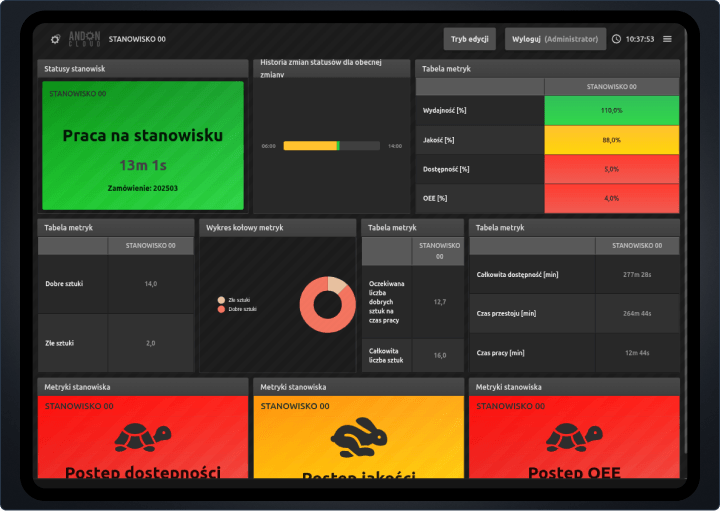
Identification of major availability and performance losses
Real-time data analysis makes it possible to immediately point out where the plan is not being implemented as intended
Matching data to planning needs
We help the client select key data and turn it into actionable metrics used in briefings and plan
Operational decision support in gemba
Support team leaders and champions with ongoing data analysis so that decisions are quick, accurate and fact-based
System
Our system is intuitive, but you can always count on us
We help your team work more efficiently every day.
Documentation
Develop your skills with our guides and tutorials to get the most out of AndonCloud.
Customer support
Get help by contacting our technical support team by phone or email.Monday - Friday; 9:00 - 17:00support@andoncloud.comMonday - Friday; 9:00 - 17:00+48 71 340 70 32
Integrations
Integrate with over 5,227 third-party apps and tools.
Have questions for our sales team?
Call us and we will guide you through the process.+48 71 340 70 15
FAQ
Frequently asked questions
How do companies today identify bottlenecks without a system?
Most often manually or in Excel. Data is collected manually, often incomplete and subject to perceptual errors.What does real-time analysis of system data provide?
It allows you to immediately detect where the process is slowing down and who should react. The system informs specific people.Does the system itself suggest where the problem is?
Yes - the data indicate extended cycles or delayed responses, suggesting potential bottlenecks.What data sources are used for analysis?
Cycle times, UR department responses, downtime information and getting to the problem area.Is it possible to analyze data after the fact?
Yes - data is available in dashboards (live) and reports (historical).What are the typical problems with recording outages without a system?
Events are recorded after time and inaccurately - often distorted or incomplete.What does the implementation of the system change?
Instead of unplanned downtime, planned downtime occurs - because data is seen immediately and actions taken faster.Does the system allow you to categorize the causes of downtime?
Yes - it allows you to create a catalog divided into machine and human downtime, with any depth.Can comments be added to outages?
Yes - operators can describe the event to complete the information beyond the category itself.Does every customer analyze downtime the same way?
No - the analysis is tailored to the client, its work culture and operational needs.Does the system record changeover times automatically?
Partially - the system can collect data automatically, but the operator also has the option of manually marking changeover stages.What can be analyzed in changeover data?
Differences between shifts, operators, types of orders - all based on measurements.Does Andon help shorten changeovers?
Yes - together with the client we analyze the data and create standards step by step.What measures are being implemented to shorten changeovers?
Standardization of sequences, elimination of unnecessary steps, assignment of tasks to roles.Does the analysis cover all operations?
Yes - both physical activities and waiting time between stages are measured.What indicators help in production planning?
Those that show availability and performance losses. Andon helps recalculate them from system data.Does the planner use real-time data from the hall?
Yes - the production data is up-to-date and can be used immediately in decisions.Does the system account for differences between shifts or brigades?
Yes - data can be assigned to a shift, operator or machine.Is the data ready for use in briefings?
Yes - Andon, together with the client's team, helps transform the data into understandable reports.Do you support champions and team leaders in the arena?
Yes - this is an important part of deployments. Operational users get clear information and tools to act.
Optimizing manufacturing processes is not just about implementing a system. AndonCloud supports companies as a consulting partner, analyzing real data from the shop floor and helping teams make decisions. This makes it possible to detect bottlenecks, reduce changeover times and reduce downtime - not just record them.
The AndonCloud team works directly with customers - analyzing production data, identifying causes of delays, supporting planning and implementing specific improvements. The system allows you to observe workflow in real time, record response times, identify sources of losses and measure the efficiency of operations. The system automatically collects data from the line, but operators can also manually mark selected events - such as changeover steps.
Cooperation with AndonCloud is not only technology, but also methodology and consulting experience. Customers receive not just dashboards, but real decision-making support - from shift leaders to planners and maintenance. All to make production faster, more predictable and better managed.
The AndonCloud team works directly with customers - analyzing production data, identifying causes of delays, supporting planning and implementing specific improvements. The system allows you to observe workflow in real time, record response times, identify sources of losses and measure the efficiency of operations. The system automatically collects data from the line, but operators can also manually mark selected events - such as changeover steps.
Cooperation with AndonCloud is not only technology, but also methodology and consulting experience. Customers receive not just dashboards, but real decision-making support - from shift leaders to planners and maintenance. All to make production faster, more predictable and better managed.
Contact
Contact us
If you have any questions, talk to our expert
We will respond within the next business day
sales@andoncloud.comPhone
Monday - Friday; 9:00 - 17:00
+48 71 340 70 15Make an appointment
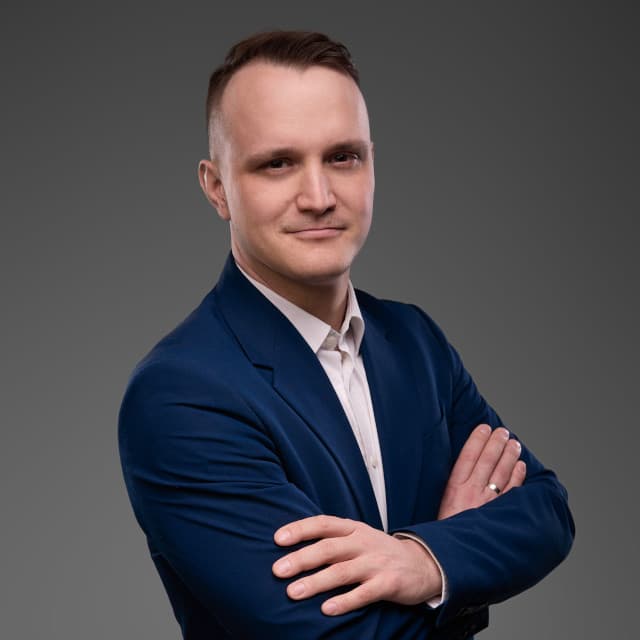
Marcin Wierzbicki
During the meeting, we will present the product and help you configure the system in your company efficiently and quickly. Our team is at your disposal.
Newsletter
Sign up for the newsletter
Want to stay up to date? Sign up for our database.
By subscribing to our newsletter, you agree to our Privacy Policy and to receive updates from our company.