Production Data
Collect data from machines, lines and systems - automatically, without burdening operators and without the need for coding.
Real-time data logging
The system collects data from machines and lines almost immediately after an event - no manual input required
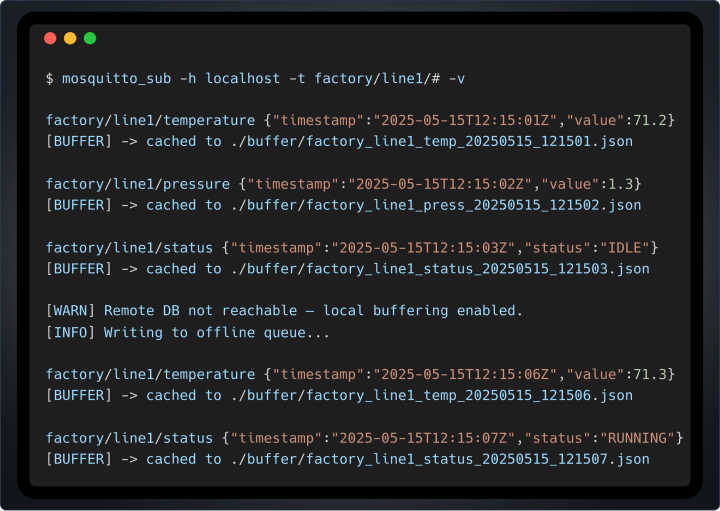
Data collected automatically from systems and machines
The system receives data from sensors, meters, PLCs and other sources. The operator does not have to click - the data is collected without his participation
Near real-time data recording
Data is saved immediately after the event or with a slight delay (push or pooling). The delays are imperceptible to the user
Data visibility for operators and managers
Operators see production data, while managers see, for example, order fulfillment or line loads, depending on the source of integration
Integration with existing systems
The system can be connected to ERP, CAD and PLC - without changes to these systems, through APIs or ready-made components
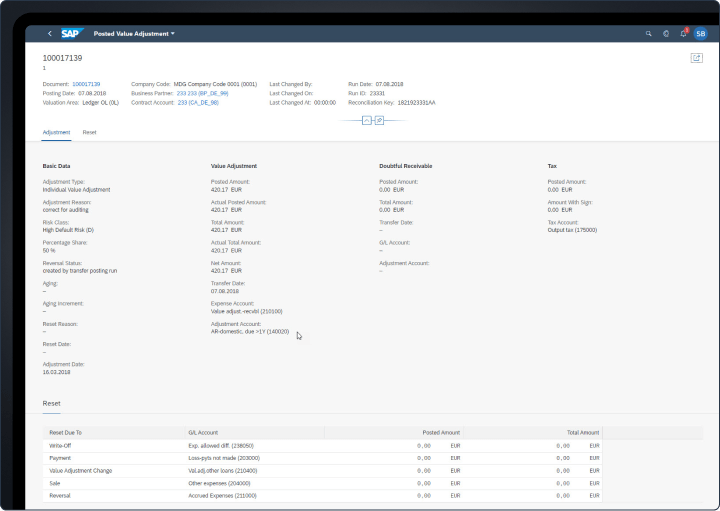
Cooperation with popular ERP and CAD systems
AndonCloud integrates with SAP, Dynamics, Odoo, Siemens, Wago, Rockwell, among others - without having to write code from scratch
Integration without changes on the client system side
Systems are connected via API, OPC UA, Modbus TCP/RTU or proprietary protocols - no need to modify current solutions
Graphics configuration via Node-RED
Integrations can be set up graphically - without coding (low code). Block editor allows you to configure data exchange processes in an intuitive way
Production data analytics
The system allows you to create custom reports, analyze OEE and visualize data in real time
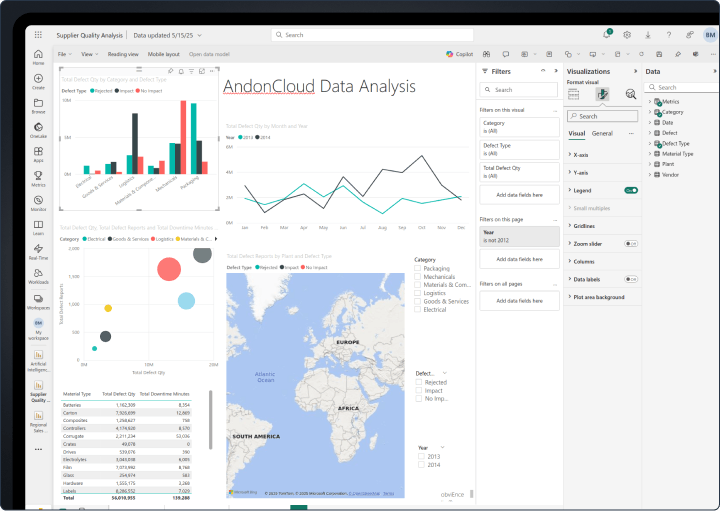
Ready-made and customizable production reports
User can create custom reports - set columns, filter data, compare shifts, products, lines or operators
Data update every 30 seconds
Production dashboards refresh automatically. This allows decisions to be made based on fresh information
Export to Power BI, Excel and other tools
Data can be exported to CSV, Excel, and integrated with tools like Power BI via API, which supports advanced analysis
Detection of anomalies and failures
The system identifies irregularities in the cycles and is the first to inform the relevant people about deviations
.png&w=3840&q=100)
Detection of performance degradation and cycle deviations
If no new art is created within a set period of time, or availability falls below a threshold - the system generates an alert
Configurable thresholds and notification types
Separate thresholds can be set for different types of data - e.g. warning, information, alarm. Each level can have its own action
Notifications to operators and leaders
Alerts go to the appropriate people via email, phone or the WMS system. This allows a response to take place immediately
System
Our system is intuitive, but you can always count on us
We help your team work more efficiently every day.
Documentation
Develop your skills with our guides and tutorials to get the most out of AndonCloud.
Customer support
Get help by contacting our technical support team by phone or email.Monday - Friday; 9:00 - 17:00support@andoncloud.comMonday - Friday; 9:00 - 17:00+48 71 340 70 32
Integrations
Integrate with over 5,227 third-party apps and tools.
Have questions for our sales team?
Call us and we will guide you through the process.+48 71 340 70 15
FAQ
Frequently asked questions
Is production data recorded automatically?
Yes - the system collects data without the operator having to click. The information comes directly from the machines and systems.How quickly does the data get into the system?
The data appears almost immediately. It depends on the method of integration - push or pooling - but the user does not experience delays.Do you need a special setup to start collecting data?
No - you just need to indicate the data source and the type of information. The rest of the configuration can be done graphically.Can the operator see the data that is being collected?
Yes - the system can show selected data to the operator on the screen or line panel, depending on the role and access level.What if the machine has no digital data output?
Other sources can be used, such as sensors, meters, interfaces or master systems that make data available cyclically.Can AndonCloud work alongside our ERP?
Yes - the system integrates with ERP without modifying it, such as through API or dedicated connectors.Do you need to have your own IT department for integration?
No - you can do the basic integrations yourself, thanks to the Node-RED editor. AndonCloud also supports deployment.Does the system work with our PLCs?
Yes - the system supports popular protocols like Modbus TCP/RTU, OPC UA and many others available on the market.How long does it take to connect to an existing system?
Usually a few days - depending on the number of data sources and the type of connection. Some of the integration can be ready on the spot.What if our system doesn't have an API?
Other forms of integration can be used - via database, CSV files, OPC or reading physical signals.Do I need to know how to program to analyze data?
No - reports are created graphically. You can add columns, filter data, compare changes without knowledge of SQL.What reports can I generate from the system?
OEE reports, cycle times, operator productivity, comparisons between lines or shifts. The system allows data to be filtered by any parameters.Does the system refresh the data on a regular basis?
Yes - dashboards update automatically every few tens of seconds, without the need to refresh manually.Can I also analyze the data outside the system?
Yes - data can be exported to CSV, Excel or linked to Power BI and other external tools.How can I compare data between products or operators?
Just use the filters in the report - you can put together any variables and compare them over time or between changes.Co system uważa za anomalię w produkcji?
E.g., failure to produce a piece at a certain time, a drop in cycle rate, downtime or unexpected changes in parameters.Can I set the thresholds that trigger the alarm myself?
Yes - each data type can be assigned a separate warning and alarm threshold. Different responses can also be set.Does the system just display the message, or does it inform people?
The system sends email or SMS notifications or forwards them to other systems - such as WMS or CMMS.Can the operator acknowledge the alarm or add a comment?
Yes - the interface allows you to approve an alarm, add a reason, comment or assign a task.Does the system show a history of detected anomalies?
Yes - all alerts are saved and can be analyzed later in reports or dashboards.
Automatic collection of production data helps streamline the work of operators, planners and supervisory teams. The AndonCloud system captures data without human intervention - information comes in from machines, sensors, PLCs or other systems without the need for manual input. Data is collected almost in real time, and its visibility can be customized according to the user's role - from operator to production director.
Integration with existing systems is done through standard communication protocols, APIs or files. There is no need to modify ERP, PLC or WMS - connections are configurable in a graphical editor. AndonCloud supports integration with SAP, Siemens, Rockwell and many other solutions used in industry.
Collected data can be analyzed in the system or exported to Power BI and Excel. Users create custom reports, compare shifts and products, analyze OEE and cycle times. The system also enables automatic detection of anomalies and cycle deviations. With notifications sent to the right people, it is possible to react quickly and reduce the impact of failures.
Integration with existing systems is done through standard communication protocols, APIs or files. There is no need to modify ERP, PLC or WMS - connections are configurable in a graphical editor. AndonCloud supports integration with SAP, Siemens, Rockwell and many other solutions used in industry.
Collected data can be analyzed in the system or exported to Power BI and Excel. Users create custom reports, compare shifts and products, analyze OEE and cycle times. The system also enables automatic detection of anomalies and cycle deviations. With notifications sent to the right people, it is possible to react quickly and reduce the impact of failures.
Contact
Contact us
If you have any questions, talk to our expert
We will respond within the next business day
sales@andoncloud.comPhone
Monday - Friday; 9:00 - 17:00
+48 71 340 70 15Make an appointment
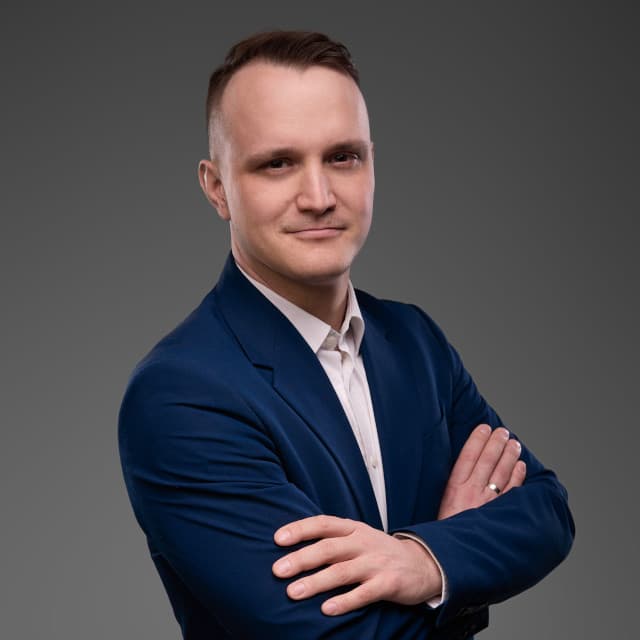
Marcin Wierzbicki
During the meeting, we will present the product and help you configure the system in your company efficiently and quickly. Our team is at your disposal.
Newsletter
Sign up for the newsletter
Want to stay up to date? Sign up for our database.
By subscribing to our newsletter, you agree to our Privacy Policy and to receive updates from our company.